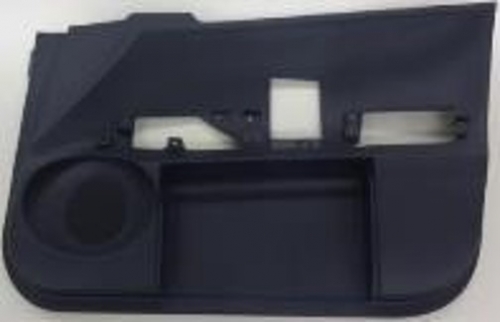
- Mobility
- Sustainability
High-magnification foam mold technology
Injection Molded Products Utilizing foam mold technology
- Mobility
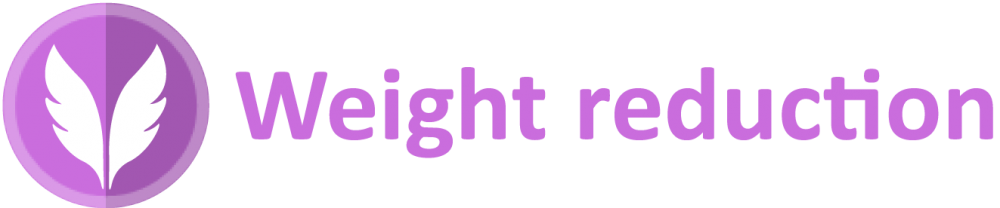

Pursuit of further weight reduction for EVs
Foamed plastics are increasingly adopted as a material that contributes to energy saving and weight reduction of automobiles.
For instrument panels and door trims, it is required to achieve both light weight as well as texture in terms of surface design and a pleasant feeling to the touch.
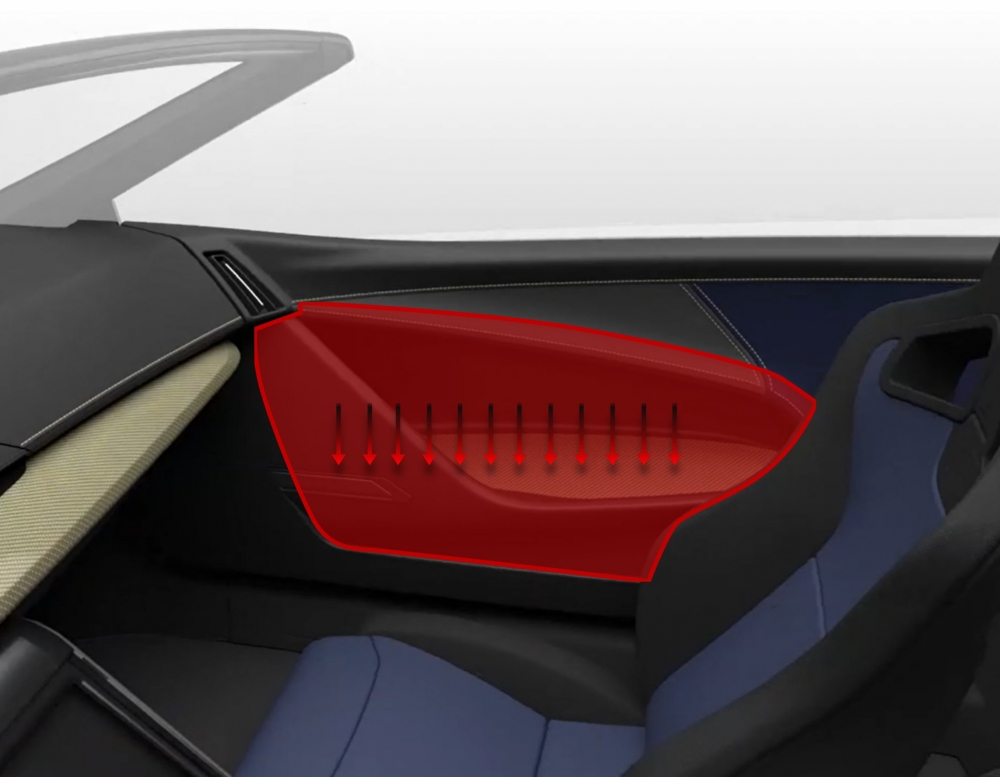
Lightweight by foaming technology
Injection foam molding technology of PP resin is used to form the core (foamed) layer and the skin layer.
SEKISUI’s proprietary technology enables high-aesthetic appeal, high-shock resistance, and high rigidity, while reducing weight by 25-35% compared to solid resin parts.
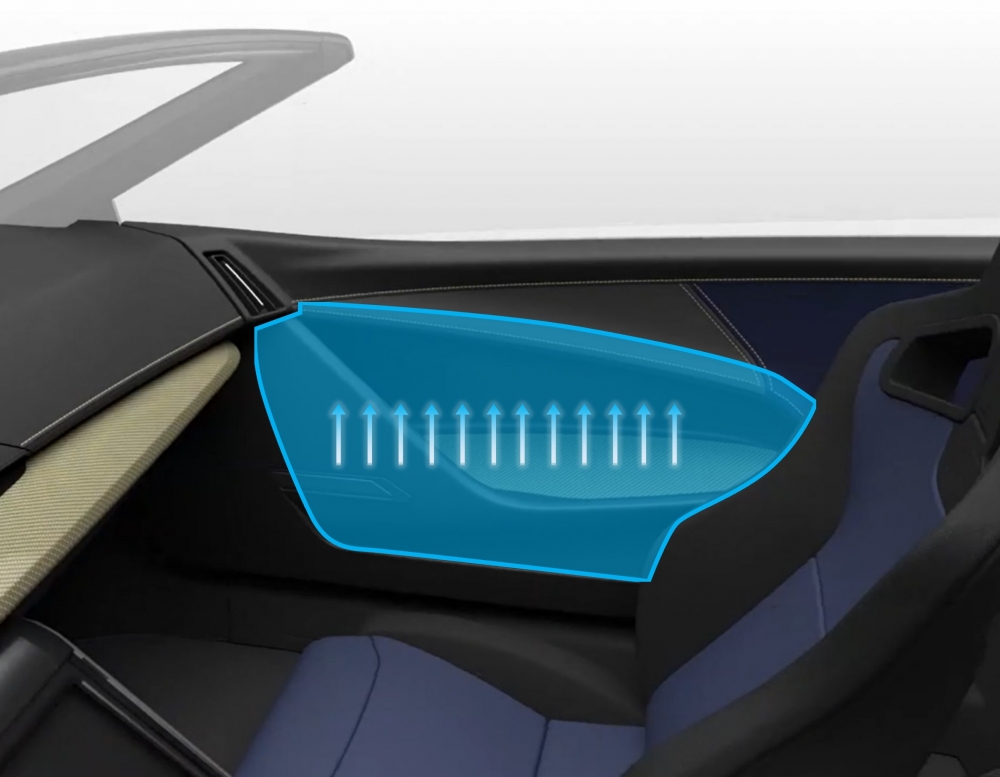
Technical information
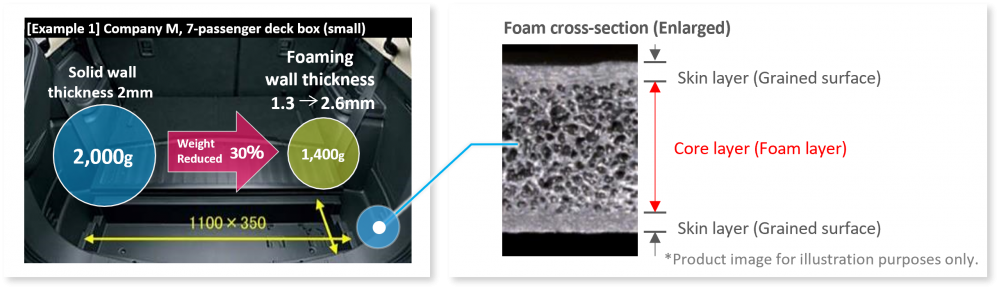
Technical overview
Foam injection mold with all-purpose
PP-based compound resin
Injection molding method (Electric motors)
The mold core-back method releases foam components accumulated in the resion to form the core (foaming) layer and skin layer.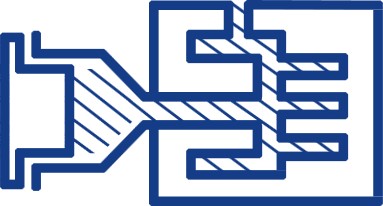
Lightweight foam mold
Automobile interior materials
25~35% weight reduction
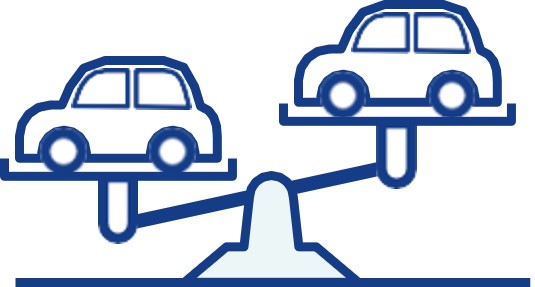
Integration of three unique technologies Beautiful appearance,
high impact-resistance and rigidity
Fusion of 3 technology
- Material formulation : Appropriate formulation of all-purpose PP resin
- Mold/Product design : Uniform filling design
- Molding technology : Stabilization of quality
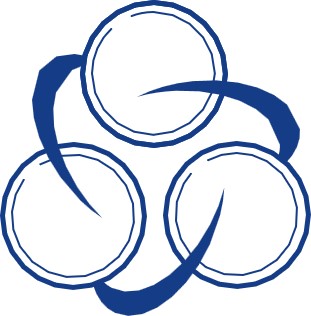
Promising applications
Automobile interior parts, etc.
- Interior trim(Door and deck side)
- Luggage box
- Under-seat
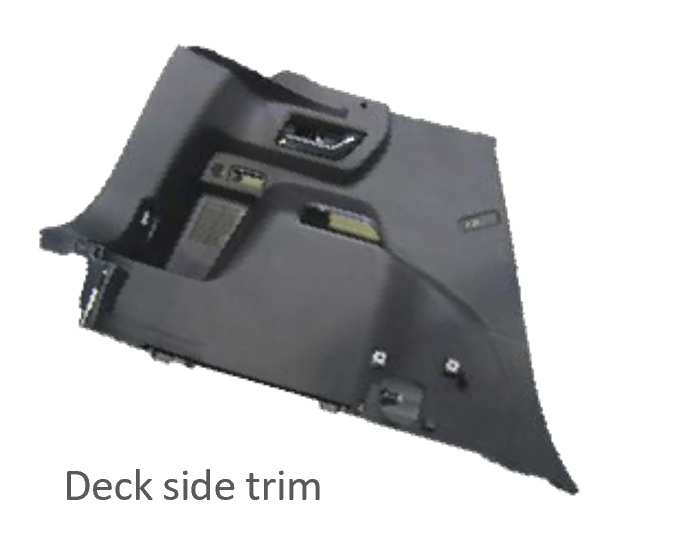