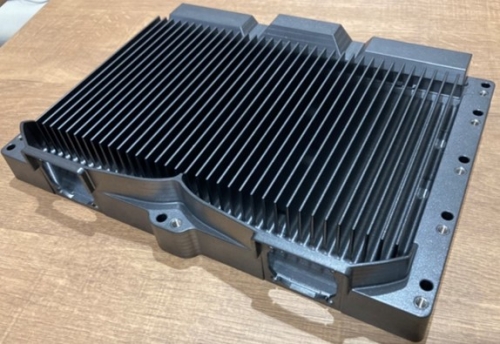
Injection molding with thermal-conductive and EMC shielding
- Mobility
- Malfunction prevention due to high temperature and electromagnetic noise
- Molded plastic products to prevent thermal runaway and electromagnetic interference
- Techinical information
- Document download


Malfunction prevention due to high temperature and electromagnetic noise
With the electrification of automobiles and the introduction of advanced driver assistance systems (ADAS), the number of onboard electronics in vehicles is increasing, along with the sources of electromagnetic noise and heat.
Due to the risk of electromagnetic noise causing malfunctions and accidents with onboard electronics and automobiles, it is essential to take electromagnetic compatibility (EMC) measures such as preventing the emission of electromagnetic noise, ensuring resistance to the effects of electromagnetic noise, and ensuring proper operation even under the effects of electromagnetic noise.
While metal materials are excellent in electromagnetic wave shielding and heat release properties, they are heavy and difficult to fabricate, resulting in a growing need for alternative materials to metal for onboard electronics for vehicles, where weight reduction is essential.

Molded plastic products to prevent thermal runaway and electromagnetic interference
Our injection molding with thermal conductive and EMC shielding is a high-performance thermoplastic resin molding product that protects electronics from problems by preventing thermal runaway and electromagnetic interference.
Injection molding enables flexible shaping, and the resin is about 45% lighter than aluminum, contributing to heat release and EMC measures as well as weight reduction by replacing metals.
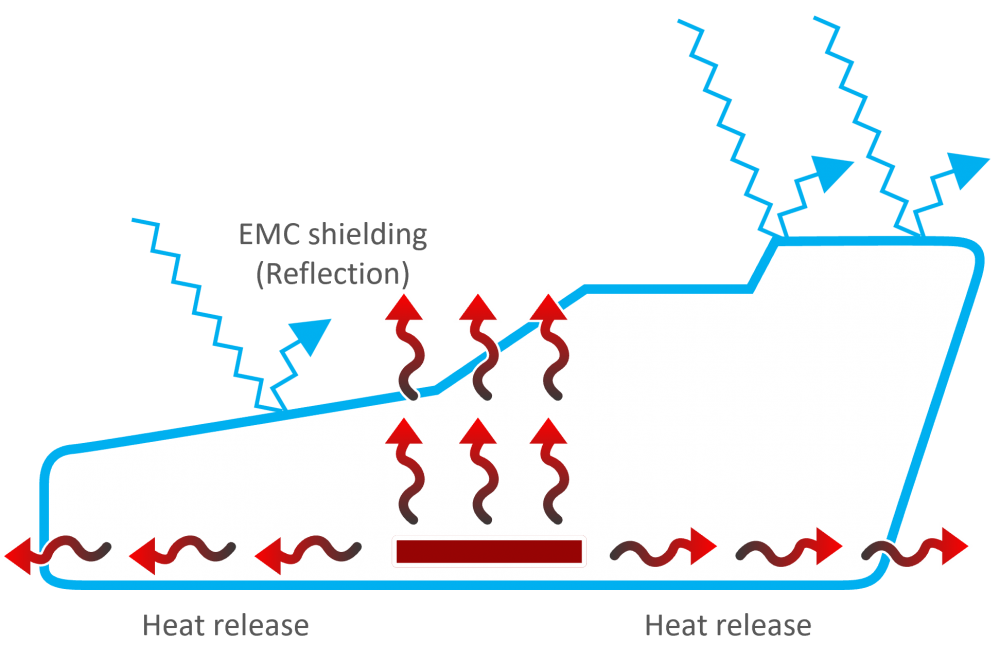
Techinical information
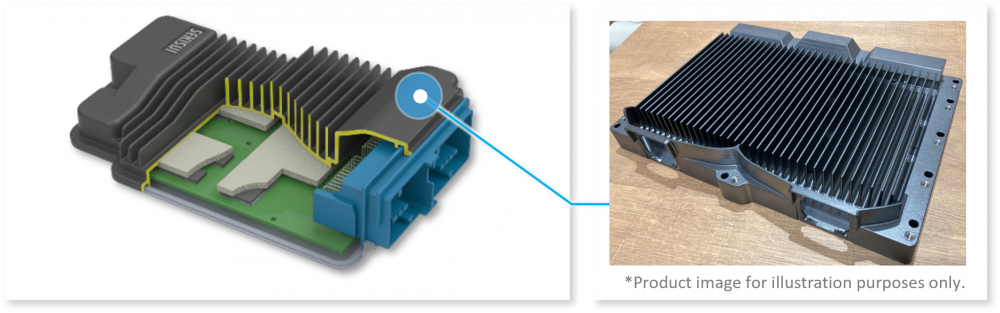
Technical overview
Easy molding
Mold injection
Two-Colour molding guaranteeing heat dissipationperformance with complex shapes/thin walls.
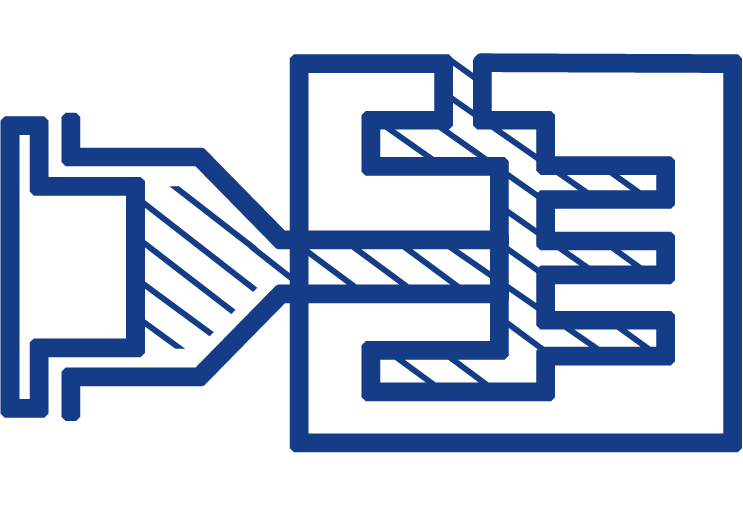
Light weight
About half the weight
Approximately 45% lighter than metal.Many applications and contributes to weight reduction of automobile.
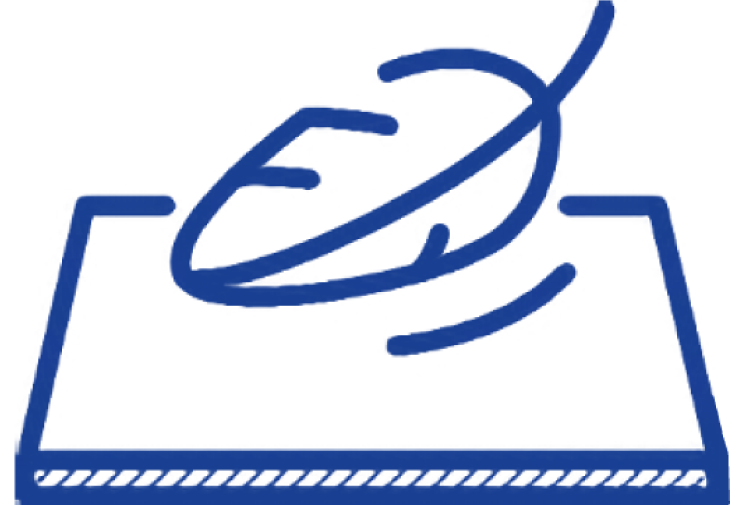
EMC shielding + heat radiating
With thermal-conductive resin
Efficient heat sink processing shape achieves heatdissipation performance equivalent to aluminum.
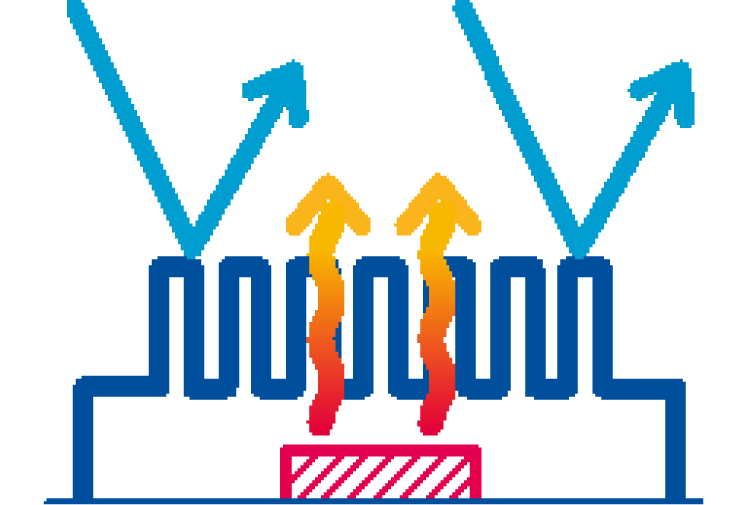
Process efficiency
Cost effective
Reduction of parts count, process simplification,and reduction of maintenance frequency.
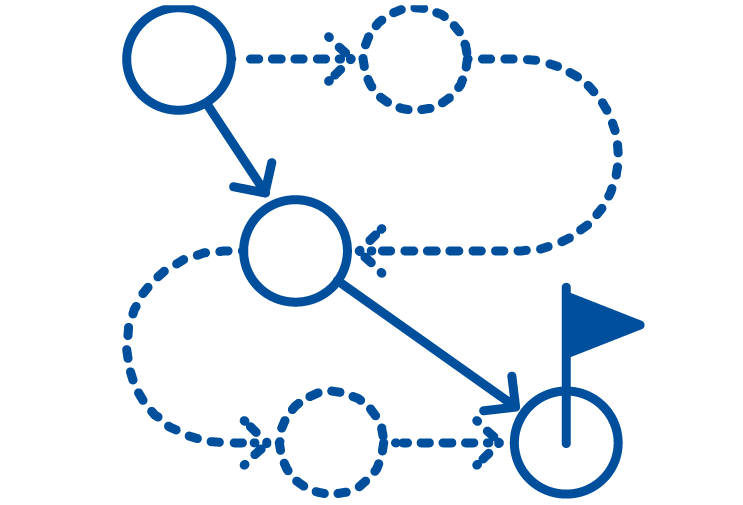
Technical details
Easy molding
Design of complex shapes and ultra-thin fins
Mold injection enables design of shapes that can be expected to have high heat dissipation. Integral molding also reduces the number of parts.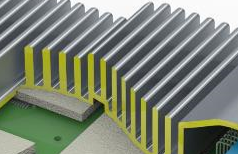
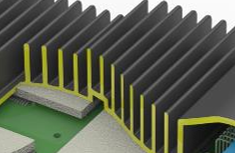
Multi-functionalization by two-Colour molding
Can be arranged to meet your needs. Only a part of a component can be two-Colour molded, and a function can be added only to that part.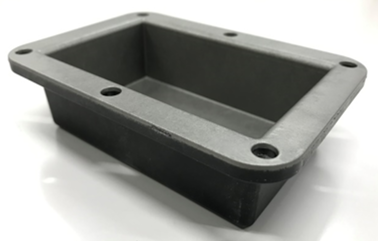
Light weight
Resin is about 45% lighter thanaluminum. Total weight of control box is calculated as 5 large units and 30 small units per automobile.
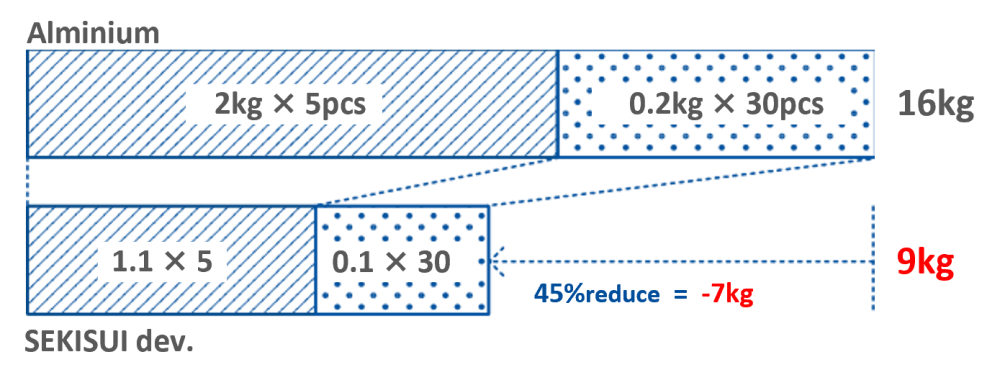
EMC shielding + heat radiating
EMC shielding effectiveness test
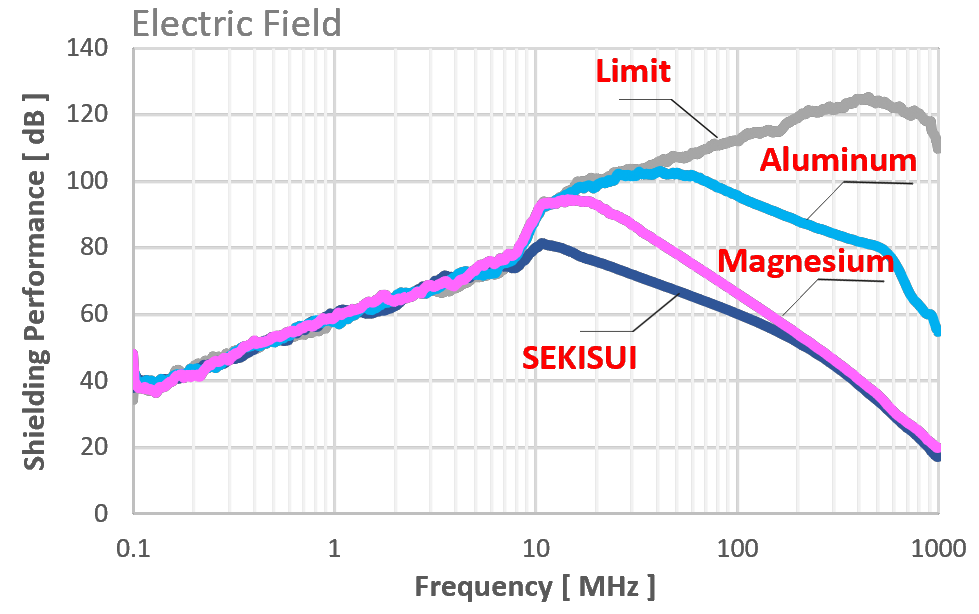
Heat radiation test
[ Test condition ] Ceramic heater:3.1W | Heat radiationg grease:3.8W/ [m-K].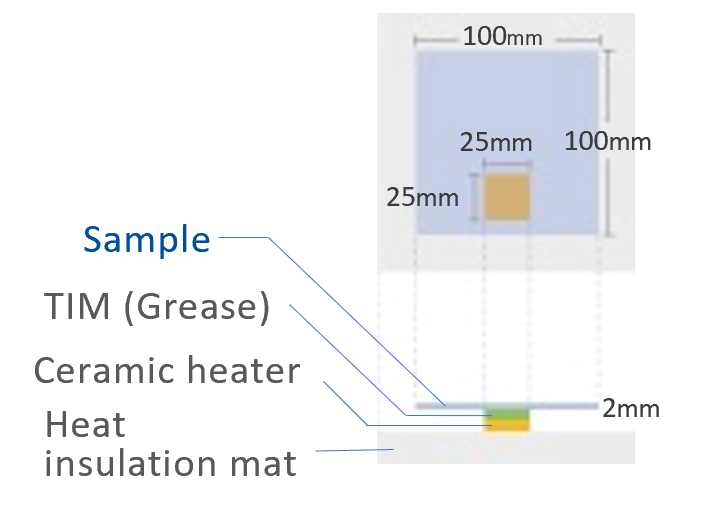

Process efficiency
The number of automobile parts itself can be reduced, and the production process can be reduced due to the characteristics of the material. And man-hour efficiency can be improved by reducing the number of times production equipment maintenance is required.- Reduced mold wear and frequency of mold replacement
- No post-processing required (Blast-free)
- No anodizing required
Possibility of 15% improvement In comparison with aluminum
Document download
- All
- Catalog
Name | Type | File | Update | File |
---|---|---|---|---|
Catalog:Injection molding with thermal-conductive and EMC shielding_SekisuiMobilitySolution | Catalog | 2023-09-11 | Download1.30 MB |